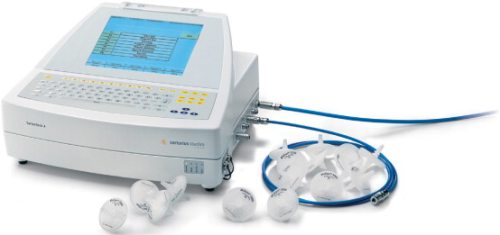
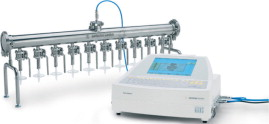
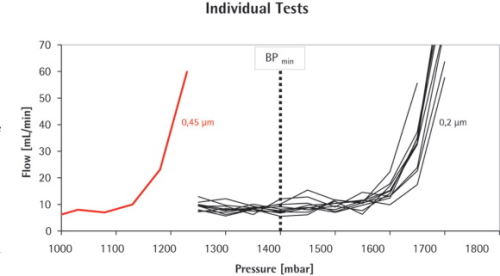
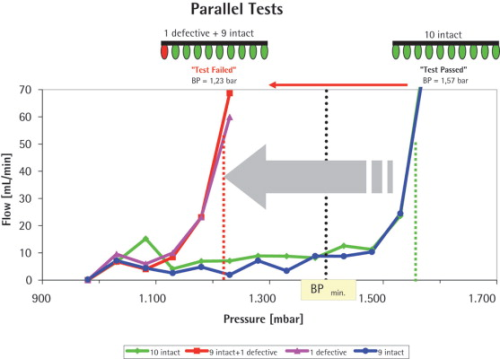
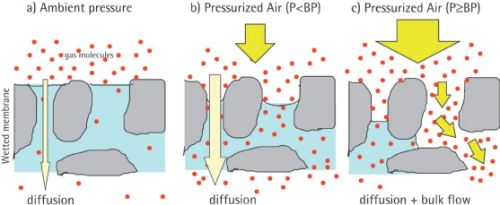
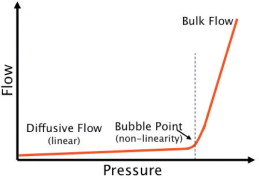
Introduction
Sterilising grade venting filters are used to avoid the potential risk of air-borne germs contaminating containers such as fermenters or cell-culture vessels. Sterilising grade filtration can only be guaranteed when the filters used are tested for integrity. Therefore, those relatively small venting filters are often tested by the bubble point test. Depending on the program settings and the actual bubble point (BP), it can easily take 10-20 min to perform one such test on the filters. When large quantities of filters are used and tested every day, any improvement regarding the required time would be beneficial as soon as it is guaranteed that there is no increasing risk of overlooking defective filters.
This article describes a method by which small venting filters (filtration area - 20 cm²) can be tested efficiently by means of parallel testing. This parallel testing method drastically reduces the time required for testing, in turn yielding a clear economic benefit for users without compromising safety.
Bubble point tests
Small venting filters (Midisart 2000 from Sartorius Stedim Biotech) with a pore size of 0.2 μm and an effective filtration area of 20 cm² type were used for this investigation to perform bubble point tests using the parallel method. In order to prove their ability for detecting a single defective filter within an array of ten filters in a parallel arrangement, one filter of pore size 0.2 μm was replaced with a filter with pore size 0.45 μm. The theory behind this set up was that, although the 0.45 μm filter was perfectly intact and within specification for 0.45 μm filters, it should not pass the integrity test run on bubble point limit values for 0.2 μm filters. If this theory applied, the question would then be to determine if it is possible for an automatic integrity tester to reliably detect the out-of-specification filter between the 0.2 μm standard filters.
An essential prerequisite for performing bubble point tests is that the membrane is wetted completely with a suitable wetting liquid. Because the PTFE membrane of the filters is extremely hydrophobic and not spontaneously wettable by water, a 60% mixture of isopropyl alcohol (IPA)-water-mixture was used for wetting the membranes. In order to flush each filter with 20 ml of 60% IPA, a disposable syringe was used to apply the wetting solution in the direction of filtration. Because the testing procedure forced wetting liquid out of the pores, any filters used for repeated testing were re-wetted in the same manner to avoid any effect on the test results.
In the first step, the filters were wetted and then tested individually using the Sartocheck 4 automatic integrity tester from Sartorius Stedim Biotech. The test results were documented electronically and additionally printed out on paper. In the second step, the same filters were mounted on the Midisart manifold containing an array of ten filters and the manifold was subjected to a parallel bubble point test using the same test unit. The results were documented.
In order to show that it is possible to detect a single defective filter among nine others, one Midisart 2000 filter with pore size 0.2 μm (min BP = 1.4 bar) was replaced with a Midisart 2000 filter with pore size of 0.45 μm (min BP = 0.9 bar). Then, the complete manifold with nine intact plus one assumedly ‘defective’ filter was tested. Although the 0.45 μm filter was intact, it should theoretically be identified as defective within the specification for the 0.2 μm filters (BP < BPmin).
The following test parameters were set:Stabilisation time: 5 minMin. BP: 1.4 barMax. BP: 1.8 bar
Before testing all filters separately the test series was started with a leakage test to prove the validity of the complete test setup. For this purpose, all valves of the test manifold were closed and a pressure hold test (P = 2 bar, t = 5 min.) was run with the integrity tester Sartocheck 4. The pressure was kept stable during the test without any signs of leakage.
Results
An average bubble point of 1.69±0.025 bar was found for the 0.2 μm Midisart filter, while the 0.45 μm version had a significantly lower BP of 1.23 bar. This meant that the 0.45 μm filter failed the test as soon as the BP limit (BPmin) for the 0.2 μm filter was used as test criterion.
The parallel test of the ten ‘intact’ Midisarts resulted in aall of 1.57 bar. This value correlates well with the BP values measured for the individual filters. The test was classified as ‘test passed’ and therefore all ten filters showed integrity.
In the next step where one ‘intact’ Midisart was replaced with the ‘defective’ filter (0.45 μm) and the array of the ten filters (nine ‘intact’ plus one ‘defective’ with a low BP) was subjected to a BP test at the identical test parameter settings, the test resulted in a BP of 1.23 bar and the test was classified as ‘test failed’. The BP value of all ten filters was clearly defined by the filter with the lowest BP (1.23 bar) which was the so-called ‘defective’ one. This meant that the ‘defective’ filter was successfully detected when ten filters were measured in parallel.
In order to confirm this result, the defective filter was pneumatically decoupled by closing the connected valve and the remaining nine intact Midisarts were retested after re-wetting. This test resulted in a BP of 1.57 bar, i.e. it was identical to the test result obtained when all ten ‘intact’ filters were tested.
Discussion
The Bubble Point Test
The bubble point is defined as the pressure at which the wetting liquid is forced out of the pores, thereby creating bubbles. By increasing the pressure on the upstream side, the differential pressure increases and finally overcomes the capillary forces to consequently press water out of the pores of the filter.
Below the bubble point pressure, only diffusive flow through the wetted pores takes place. The amount of diffusive flow is relatively low, whenever a linear relationship exists between test pressure and air flow rate. When the test pressure is increased incrementally to the bubble point, the air flow starts to increase over-proportionately because diffusive flow occurs at this point in parallel with bulk flow through opened pores. This bulk flow is much greater than the diffusive flow and can be used to detect the bubble point. In principle, the automatic integrity tester checks the air flow by measuring the pressure decay in the filter housing on the upstream side of the filter. The test pressure is increased in increments of 50 mbar and the air flow rate is measured for each step. The resolution of the bubble point measurement is limited by the size of the increment (±50 mbar). The test device determines the point of over-proportional increase of the air flow using internal algorithms. This is exactly the point where the pores open and enhanced flow starts. The integrity tester uses this pressure as the bubble point.
The bubble point therefore reflects the pore size of the largest pores within the membrane, namely because the pores with the largest pore diameter offer the lowest capillary forces and the liquid is removed more easily than through smaller-diameter pores. This fact makes sense because exactly those large pores offer a risk for micro-organisms to pass the membrane.
It should be mentioned that the bubble point per se does not tell anything about the retention capabilities of the membrane, but is only a robust physical test. In order to determine the retention capability of a filter, sophisticated microbiological tests must be performed and correlated with the results of the integrity tests. Such tests are performed by the filter manufacturers during filter validation. Filters have to pass the bacterial challenge test (BCT) which means they must be able to produce a sterile filtrate after filtering a test solution containing 107 bacteria (Brevundimonas diminuta) per cm2 filter area [[1] and [2]]. The limit value (BPmin) is defined when correlating the test result of the BCT (test passed or failed) with the BP of the same filter and adding a specific safety margin.
As soon as the BP of a filter drops below the limit value (BPmin), sterile filtrate or sterile air filtration cannot be guaranteed. Consequently, such filters may not be used in pharmaceutical production process. The facts discussed underline the critical importance of filter integrity testing within biopharmaceutical production processes. Therefore, it is necessary to identify reliably defective filters within a multiple-filter arrangement and parallel integrity testing.
Identification of defective filters
Obviously, a failed filter integrity test does not identify which of the parallel tested filters is the defective one. Consequently, all ten filters have to be tested individually to achieve safety.
The test manifold was designed to allow a different approach. Its short tubes can be connected to the hose barbs of the filters and the other end can be hung in a water bath. The bubble point test is started and the test pressure is reached; the reduced diffusion-driven air flowing through the wetted membrane causes the air bubbles to come out of the tube slowly. As illustrated, the bubble point is characterised by a disproportionate increase in air flow. This sudden increase in flow can be visualised by a sudden increase in air bubbling out of the tube. A defective filter reaches the BP earlier and can be identified simply by observing the air bubbles that leave the different tubes. As soon as the defective filter is identified, it can be pneumatically decoupled from the manifold by closing the valve and the remaining nine filters can be tested afterwards. The parallel procedure avoids all ten filters having to be tested individually.
In this context, it is important to note that a failed test does not automatically mean that a filter is really defective. When filters repeatedly fail integrity testing, the correct wetting of the membrane should be checked. A membrane that is not perfectly wetted will definitely fail the test although the membrane itself is functioning properly within its sterilising grade. In such a case, the wetting procedure should be improved and the test repeated.
Conclusion
The data presented clearly show that a single defective filter reliably leads to a failed integrity test when tested in a multiple arrangement together with nine intact filters. The relatively small filtration area of 20cm² produces a low diffusion rate for the single elements. In this situation, the masking effects common with larger (pleated) filter elements play a negligible role. When more than one filter is tested for integrity, the filter with the lowest bubble point determines the BP of the multiple filter arrangement. This observation underlines the safety of parallel testing such small filters and proves that a defective filter will lead to a failed test. The time required for the testing procedure can thereby be reduced by 90%. This allows more filters to be tested in a given time frame which generates an economic benefit for users.
References
1 ASTM, Committee F 838-05. Standard test method for determining bacterial retention of membrane filters utilized for liquid filtration, ASTM, West Conshohocken, PA (2005).
2 HIMA, Microbial evaluation of filters for saterilizing liquids. Document No. 3, volume 4, Health Manufacturers Association, Washington, DC (1982).
Uncited reference
Parenteral Drug Association. Technical Report 26: Sterilizing Filtration of Liquids.