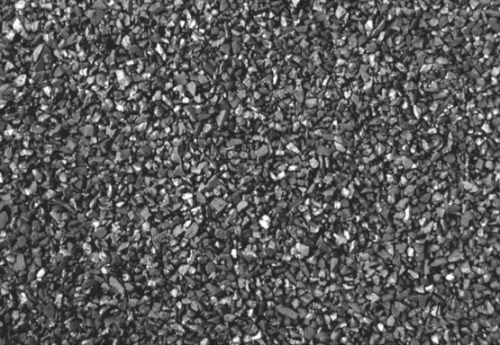
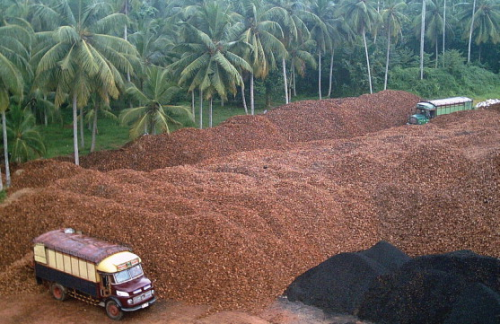
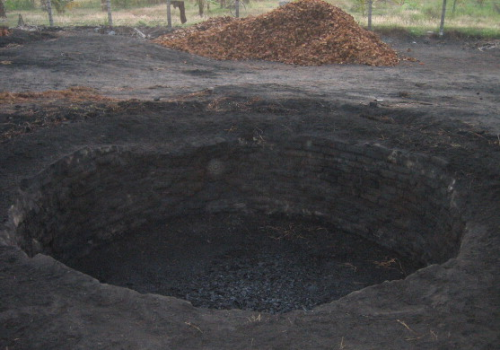
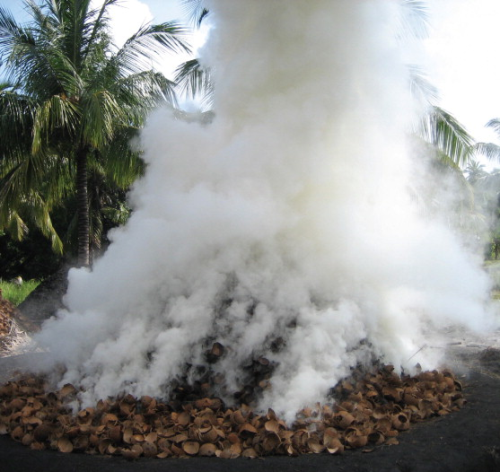
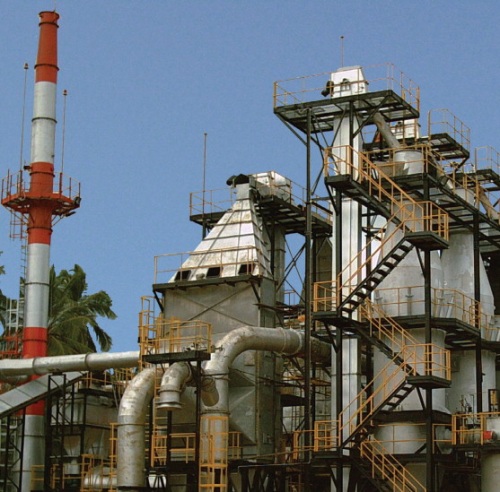
A pdf version of this article is available on the right-hand side under 'Downloads'
Essential raw materials for the manufacture of activated carbon are charcoal and fuel oil. One source of charcoal is coconut shell and Haycarb PLC is the leading producer of coconut shell activated carbon. Eurocarb Products Ltd is the European subsidiary of Haycarb. The company has developed the Recogen project in Badalgama, Sri Lanka, which is a fully automated industrial process for producing charcoal and electricity from coconut shells. The process has been designed to replace traditional pit charcoaling methods that have an adverse effect on the environment.
Activated carbon
Activated carbon, alternatively known as activated charcoal or simply active coal, is a highly porous form of carbon used extensively in purification and filtration technologies as a sorbent media. The applications of coconut shell activated carbon can be found in a variety of diverse industries ranging from point-of-use water filters, respirators, solvent recovery and gold mining.
In addition to coconut, activated carbon can be derived from a variety of carbonaceous raw materials including coal, peat and wood sources. Following the activation production process, different raw materials exhibit varying inherent properties in the final product resulting from the ensuing microporosimetry. Coconut shell activated carbon has a very high number of micropores making it superior to coal grades for the removal of smaller organic compounds, low boiling point chemicals with strong odours and dechlorination applications. This determines its role as the material of choice for manufacturers of water filters and respirators. On the other hand, coal-based carbons are characterised by a higher prevalence of meso and macro pores lending suitability to applications such as dye removal where larger colour compounds can be successfully adsorbed. Despite these distinct material properties there can, on occasions, be overlap between differently sourced carbons when it comes to the application's required specification.
Coconut shell, rather than coal- or peat-based material, is considered to be the greener choice; it is renewable, sustainable and easily harvested. There is no requirement for the mining or digging of non-renewable fossil fuel resources, such as coal or peat.
However, despite the extensive use of activated carbon in the purification industry for the removal of pollutants in solvent recovery, effluent control and removal of other by-products, it is not a commodity that is typically produced in an environmentally sound way.
Activated carbon manufacture
Activated carbon manufacture is generally considered a three stage process consisting of pre-activation, activation and post-activation.
• Pre-activation is concerned with quality checking and correct sizing and screening of material prior to activation. At this point material can be called kiln-feed.
• Activation is the process by which charcoal raw material kiln-feed is turned into activated carbon. Haycarb exclusively uses steam activation for this process where coconut shell charcoal is subjected to high temperatures and steam within specially designed activation kilns. Alternative manufacturing methods may involve chemical activation which requires large quantities of acid at lower temperatures.
• Finally, post-activation consists of quality checking the parameters of kiln output material. Further screening is then undertaken and additional special processes such as washing (for example, for ash/impurity removal), demagnetising and impregnation that are applied to meet the requirements of the customer's application.
Charcoaling
However, before any carbonaceous material can be turned into activated carbon it first needs to be charcoaled; this is also known as carbonisation. Charcoaling can be performed through pyrolysis (generally used for coconut shell) or as part of a chemical activation process (used for coal or wood materials). Typically, with all chemical activation processes, large quantities of acid are used which can lead to lasting damage to the environment during the disposal process dependent, of course, on the source factory's policy regarding river disposal.
Coconut shells are pyrolysed into carbon, using a method that does not employ acid. However, the practice of coconut shell charcoaling is, in coconut producing countries, a cottage industry based on standard traditional practices. In almost all cases, coconut shells are harvested and turned into charcoal through a process known as pit-charcoaling. This is a rather straightforward method where coconut shells are placed in a relatively wide and shallow pit, covered in charcoal dust, and burned under restricted oxygen conditions. This is a long-established traditional method of coconut charcoal production that can be easily witnessed in many coconut growing areas through the tell-tale plumes of white smoke. The end product charcoal is then sold to activated carbon manufacturers for quality checking and production of activated carbon. Some manufacturers may reduce quality control costs by buying pre-screened material from the pit-charcoalers direct in order to minimise pre-activation processing. This can lead to quality issues as pit-charcoalers typically sell charcoal by weight – for example, unscreened contaminants such as sand can turn to glass-like foreign matter when subjected to the high temperatures of the activation kiln and renders product unsafe for use in drinking or food related applications.
The need for a new process
The problem with this process is the pit-charcoaling method. It occurs under relatively uncontrolled conditions and releases large quantities of greenhouse gases, such as methane, along with a wide range of organic vapours and gases into the atmosphere. As an indication of scale, in Sri Lanka in 2007, approximately 130,000 tonnes of methane and other gases/vapours were released through the production of 55,000 tonnes of charcoal through pit-charcoaling. It is a practice which is under increasing scrutiny and there is the possibility that this method of charcoal production will be banned in countries where it is currently employed.
The Recogen process
In response to this environmental problem, Eurocarb's parent company, Haycarb, began the Recogen project in Badalgama, Sri Lanka. Recogen is a patented mechanised, industrial process where coconut shells are charcoaled within a specially designed reactor. Those gases that would be otherwise released to the atmosphere are collected and combusted to generate steam and in turn electricity. The project, still in its relative infancy, has the capacity to generate approximately 26,000 tonnes of charcoal per year and an electrical output of 6 megawatts.
Recogen significantly differentiates Haycarb's production process in that it allows the ability, as a manufacturer, to move backwards along the supply chain and exercise greater quality control over the production parameters of the charcoal itself. Consequently, while working with customers to determine new bespoke activated carbon specifications; the R&D teams are able incorporate specification requirements into the feedstock rather than be reliant on typical pit-charcoaling raw material.
The project operates as a subsidiary company of the parent group and is self-sufficient through the sale of charcoal material to activated carbon manufacturing and supply of surplus electricity to the National Grid.
Additionally, Recogen is approved by the United Nations Framework Convention on Climate Change (UNFCCC) under the Kyoto Protocol to trade carbon credits through the Clean Development Mechanism (CDM). This independent validation is certified by TÜV SÜD. The CDM allows emission reduction/removal projects in developing countries to earn certified emission reduction credits, each equivalent to one tonne of CO2 – these credits can then be traded and used by industrialised countries to meet a part of their emission targets under the Kyoto Protocol. Even at this stage, Recogen has the capacity to generate 46,000 carbon credits annually. In basic terms, while many businesses seek to off-set their carbon negative footprint, the Recogen project is carbon positive and is able to trade those carbon credits onwards. Haycarb intends to consolidate its commitment to new green technologies through expansion of the Recogen project and further research in to new ways to minimise the environmental impact of a key product in the applications of filtration and separation.