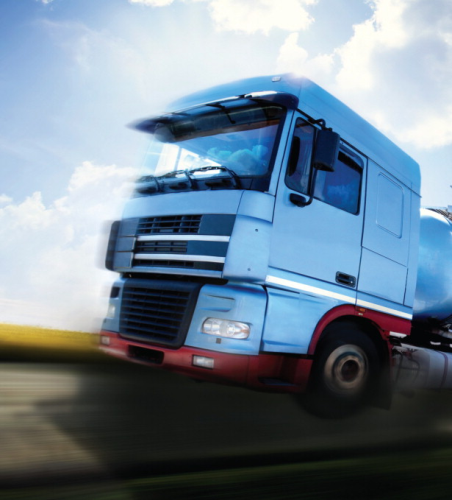
Veolia Environmental Services is the UK's waste management leader. While it is involved in numerous waste management activities across the country, one of its Sheffield sites, in Northern England, focuses on the recovery of hydrocarbons, diesel oils and industrial solvents.
One particular recovery process is the manufacturing of a secondary liquid fuel (SLF) from liquid wastes. These materials come from various sources, with the majority from the manufacturing industry and include waste fuels, waste thinners, waste paint, waste oils and waste solvents. The waste materials are carefully recovered by Veolia and then blended, macerated, and filtered under strictly regulated conditions before being delivered to cement manufacturers. As the fuel is processed to such high standards, and has to conform to strict parameters set by the Environment Agency, its combustion characteristics mean it burns cleaner than traditional fossil fuels commonly used to power cement kilns. This in turn helps the cement manufacturers with their efforts in reducing their carbon footprint.
After the mixing and blending process, some debris remains in the resultant fuel oil. The debris must be removed before the fuel can be used and pumped into delivery tankers. Veolia used basket filters to achieve this check-screening function, leading to some delays in the filtering process due to blockages. Veolia realised that they required a better filtration solution that would minimise filtering time and increase employee health and safety.
After considering several options, the Veolia turned to Russell Finex. With over 70 years of experience in separation and filtration technology, Russell Finex was well equipped to conduct the necessary proving trials and ultimately streamline Veolia's filtering system.
Testing the Eco-Filters
“Russell Finex was the only company willing to provide us with a test unit before we had to commit to any equipment,” says Peter Hithersay, plant manager of the Sheffield site. “Because of this, we ran the trial unit for approximately one month before deciding that this was clearly the right choice for us.”
Veolia procured two Self- Cleaning Russell Eco Filters to filter the reclaimed fuel and immediately reaped the benefits of their installation. The filters were supplied to meet the latest ATEX approval ratings, essential to operate safely in Veolia's secured environment.
Increased productivity
The design of the Eco Filter ensures that material flow passes through the filter screen whilst the screen is automatically cleaned using a rotating wiper inside the element. The Russell Eco Filter wiper system works on a continuous basis, cleaning the filter element surface at all times thereby maintaining maximum open screen area, which in turn gives a consistent throughput rate and prevents a build up of differential pressure. Because of this unique design, Veolia is no longer experiencing filter blockages.
Productivity at the tank-filling stage has also improved by more than 50% since the installation. While filling a 28,000-litre delivery tanker with fuel used to take between 1.5 to 2 hours due to continual stoppages to clean out the filter baskets, this can now be achieved in only 25 minutes with the Russell Eco Filter. Additionally, their operators are working in a much safer and more efficient environment. “A major benefit of the installation has been the improved morale of our operators whose working conditions have changed for the better,” says John Jarvis, engineering manager.
An unexpected benefit of the filters was the satisfaction of Veolia's end customer, the cement manufacturers. Whereas previously, contaminants would very occasionally remain in the fuel and block the tanker outlet off-site, this has now ceased. Some of the cement companies used to filter the fuel at their site after receiving it, but the quality of the fuel is now so high that there is little to no need for this activity. The filters have also helped Veolia increase their overall throughput.
“Since their installation two years ago, each filter has processed about 40,000 tons of material, with no serious breakdown,” says Jarvis. Before the filters were installed, about 16,000 to 17,000 tons of fuel were passing through our plant on a yearly basis. Now, we are achieving volumes of about 50,000 tons a year, something which we would have struggled with without the Eco Filters.”