Mitigating the effects of climate change requires decarbonization on a truly global scale. This involves the removal of carbon emissions from every industrial process and the global energy supply: an imperative that is driving innovation in carbon capture, utilization and storage (CCUS). The utilization element is key. It makes practical, environmental and economic sense to reuse captured carbon dioxide (CO2) wherever possible. Applications already exist in food and chemical production, refrigeration, fire suppression and renewable fuels – but reuse depends on producing the right quality of gas.
CCUS is a broad term for various technologies designed to capture CO2 emissions from point sources such as power plants and industrial facilities, preventing their release into the atmosphere. They range from efficient compression and underground gas storage to the myriad established and evolving technologies for CO2 reuse/recycling. Filtration plays a pivotal role in all stages of the CCUS process, from decontaminating the source gas, through CO2 capture, and onwards to compression, transportation, and eventual storage or reuse.
Store or reuse?
Techniques for separating CO2 from gas streams are well-established. Tried and trusted capture technologies, such as using solvents and membranes, are being adapted to improve CCUS efficiency.
However, permanent CO2 storage is challenging. Identifying and assessing potential storage sites can be time-consuming and expensive, and even if the geology is suitable, the site may need further adaptation and continuous monitoring to prevent leakage.1 Transportation complicates the process, as building, monitoring, and maintaining the necessary infrastructure incurs significant costs.
Utilization can be a more economical alternative because established markets for CO2 already exist. Others, such as using CO2 as the primary feedstock for e-fuels production, are undergoing rapid development. Reusing CO2 in other industrial processes creates a value stream rather than a regulatory or financial burden and supports broader sustainability objectives2. Whatever the desired outcome, the quality of the captured CO2 is crucial – and this is where filtration technology plays a critical role.
Filtration during capture
CCUS projects primarily focus on capturing CO2 emissions from point sources. Capturing the gas directly from concentrated exhaust streams is more cost-effective than extracting it from the ambient air. When applied correctly, filtration maintains the efficiency of the carbon capture system and delivers the CO2 to downstream processes with minimal contamination.
Post-combustion filtration
Chemical absorption is the most established technology for post-combustion capture and is frequently used in power plants, cement production, and other industries that combust hydrocarbons to generate energy. Solvents like amines are employed to selectively absorb CO2 from the flue gas. The CO2-rich solvent is heated to release the captured CO2, which is subsequently compressed for transportation or storage.
Filtration safeguards the solvent from impurities in the flue gas that can cause fouling, foaming, and solvent degradation. This is essential for maintaining high per unit CO2 capture rates and preventing exhausted CO2 from escaping into the atmosphere. Removing residual organics and hydrocarbons through activated carbon filtration is also crucial. Any contamination reaching the top of the absorber column will directly affect the quality of the CO2 and impede the operating efficiency of the contactor column.
Figure 1 illustrates the primary points where filtration should be applied in a solvent absorption system.

Pre-combustion capture
Separating CO2 from the fuel before combustion occurs is commonly used in integrated gasification combined cycle (IGCC) plants, where fossil fuels are converted into syngas (a mixture of carbon monoxide, hydrogen, and CO2). The CO2 is then separated so the hydrogen can be used as a clean fuel.
Filtration is necessary to eliminate impurities like sulfur compounds, particulates, and moisture from syngas before CO2 separation. Membrane technologies, pressure swing adsorption (PSA), and solid sorbents are frequently used for CO2 removal in pre-combustion systems.
Oxy-combustion capture
Oxy-combustion entails burning fossil fuels in pure oxygen (O2) rather than air. The main combustion byproducts are CO2 and water vapour. Condensing the water vapour produces a highly concentrated stream of CO2.
An air separation unit (ASU) generates the pure oxygen needed for oxy-combustion. Filters remove impurities from incoming air to safeguard the ASU and ensure efficient oxygen production.
Direct air capture
Direct air capture (DAC), a non-combustion form of carbon capture, enables CO2 removal directly from atmospheric air. Solid DAC relies on sorbent materials with an affinity towards CO2 and uses a cycle system of adsorption and desorption. Liquid DAC uses solvents in a process based on absorption and regeneration loops.
The similarities between DAC and conventional carbon capture methods facilitate the transfer of existing filtration technologies into DAC processes for filtering the incoming air, maintaining solvent purity, and removing residual liquids before the air is released back into the atmosphere.
Supercritical filtration
Captured CO2 must be dehydrated and compressed for transport and storage, a process known as the supercritical or dense phase state. Contaminants such as water, lube oil, oxygen, and hydrogen sulfide (H2S) in the CO2 can threaten pipeline integrity, leading to corrosion and byproducts that create blockages in the pipeline.
If carried downstream, corrosion byproducts and pipe scale can foul critical equipment, such as control valves, metering stations, and high-pressure injection pumps. This results in higher maintenance costs, premature equipment replacement, and unplanned downtime. Solid contaminants can also obstruct permeable storage reservoir pore structures, increasing the energy required for CO2 injection and limiting the reservoir’s storage capacity.
When selecting filters and separators for dense phase CO2 applications, great care must be taken regarding the choice of materials, the filter sizing process, and the appropriate filtration rating. Figure 2 illustrates where filtration should be used during the supercritical phase.
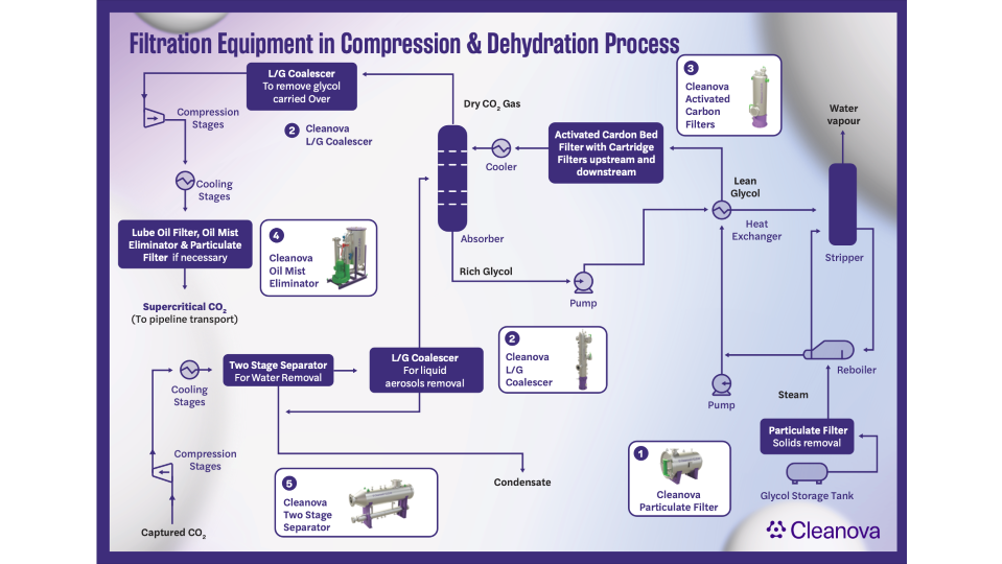
CCUS filtration developments
CCUS is a rapidly developing market. The challenge for filtration specialists is to leverage the proven advantages of technologies being used successfully in traditional natural gas applications to meet the demands of CCUS applications.
One example of success is Cleanova’s CMAX filter technology, developed for absorption-based CCUS systems. In these systems, high levels of particulate contaminants can hinder the effectiveness of solvents, leading to the clogging of downstream process equipment. Equally as critical is the removal of particulate and aerosols from the CO2 exiting the stripper process.
CMAX filters offer a market-leading solid removal capacity per unit area and are configurable across a wide range of filtration efficiencies (1 – 100µ). The technology is absolute rated and tailored to protect a range of physical solvent processes, including monoethanolamine and diethanolamine (MEA/DEA), Selexol and Purisol. It is also highly effective in supercritical CO2 injection applications where low particle concentrations are crucial for the efficient sequestration of CO2 in depleted rock formations.
However, better filtration equipment alone will not achieve industrial-scale decarbonization. Currently, there is no standard design for CCUS systems, and each application presents unique process challenges. Identifying the best filtration solution requires system designers and filtration experts to collaborate in a new way. Cleanova.C-Clean3 recognises that each process has unique parameters, and each customer has specific needs and desired outcomes. Cleanova.C-Clean gives ready access to a global pool of engineering and process expertise, alongside market-leading filtration technology. It provides tailored filtration solutions designed for each carbon capture process, based on the chosen method, load quantities, type of contaminants, CO2 concentration, pressure and temperature. The aim is to collaborate with CCUS operators from the earliest concept stages, because considering filtration requirements from the outset, within the context of the entire system design and business model, will yield the best results.
Conclusion
The successful adaptation of existing technologies like filtration to fulfill the specific requirements of CCUS operations is an ongoing process, and early collaboration is vital to the success of the decarbonization journey.
Cleanova is actively developing partnerships with process developers and licensors to ensure that new filtration technologies meet CCUS requirements now and in the future. Its pioneering approach is already yielding technological results and promoting better business practices. The company is currently exploring how filtration can evolve to meet the needs of new technologies like direct air capture (DAC) and bioenergy with carbon capture and storage (BECCS).
About the author
This article was written by Colm Joy, chief technical officer at Cleanova. It is based on the whitepaper Carbon capture, utilisation and storage: a filtration perspective, which can be downloaded here.
References
1. https://www.solartronisa.com/industries/clean-energy/carbon-capture/challenges-of-ccs
2. https://www.sciencedirect.com/science/article/pii/S1674987123001494
3. https://www.cleanova.com/cleanova-suite/c-clean/
This is a sponsored article on behalf of Cleanova.